A Battery Management System (BMS) is an electronic device responsible for managing every cell inside a battery pack and protecting the battery by monitoring its state. It achieves this by controlling the cells’ charging and discharging processes, providing an accurate estimation of battery parameters such as State of Charge (SoC), State of Health (SoH), State of Power (SoP), and Distance to Empty indication, which collectively provide valuable insights into a battery’s current condition and its ability to deliver power. A BMS can monitor the voltages of each series branch, detect an imbalance, and bring each cell to an electromotive equilibrium.
With advanced algorithms, monitoring techniques, and mathematical models, battery state estimations enable us to make informed decisions regarding energy management, battery charging/discharging strategies, and overall system optimization. In this context, understanding battery state estimations is vital for unlocking the full potential of battery-powered devices and advancing energy storage technologies.
The BMS can also monitor the battery’s temperature by collecting data from sensors attached to various corners inside the pack and sense the incoming and outgoing currents between the battery and the charger or the load. By collecting the voltage, current, and temperature data, the device makes predictable, informed, and calculated decisions to operate the battery pack within its safe operating region.
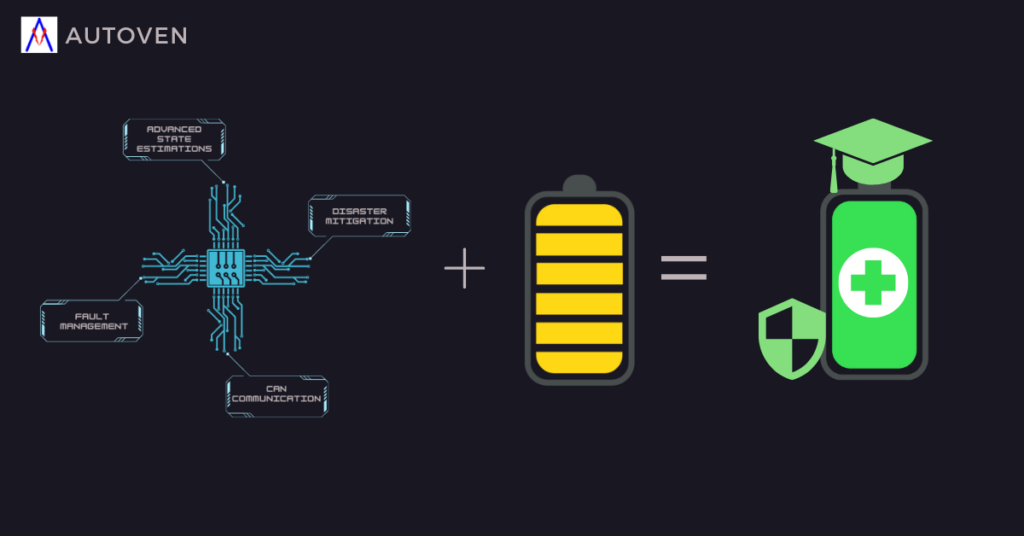
In case of events such as overheating of the battery, short-circuit at the terminals leading to over-currents, over-voltage due to excessive charging (either due to improper usage or due to high ambient temperatures), and under-voltage due to deep discharging, the BMS has to protect the battery by immediately cutting it off from the charger or the load and also begin the mitigation processes such as managing the temperatures using a cooling system, if any.
In general, a BMS is responsible for prolonging the life of a battery pack by protecting it from all kinds of electrical and thermal mishaps and guarantees the best possible performance from the battery at all times.
What does a Battery Management System do?
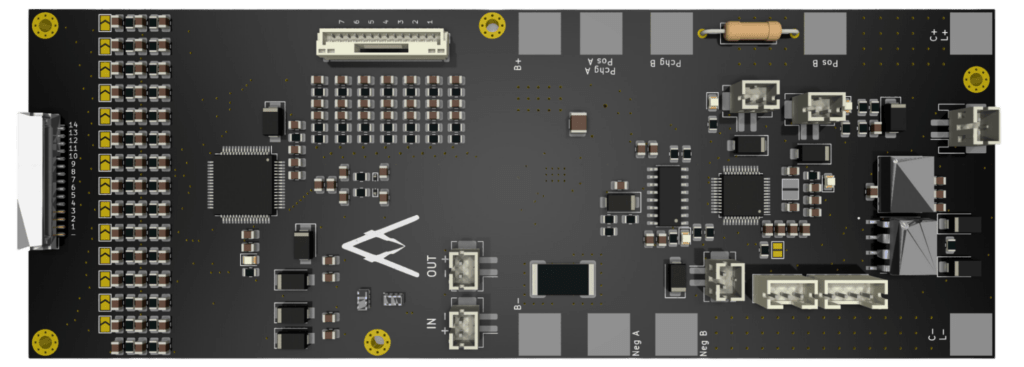
The crucial tasks that any BMS undertakes are:
- Sensing the voltages (of each cell and the battery pack)
- Sensing the currents (charging and discharging)
- Sensing the temperatures (from sensors at multiple locations inside the battery),
- Computing faults (over/under voltages, over-currents, short circuits, over/under temperature, earth insulation monitoring, and critical metrics.),
- Isolating the battery pack from the charger/load upon fault detection.
These tasks ensure the battery pack’s safe and fault-free utilization. Additionally, the BMS estimates various battery parameters by analyzing the elementary cell-level information, like voltage, temperature, and currents. These estimations are the SoC, SoH, SoP, and DTE.
- State of Charge (SoC): This factor conveys the instantaneous amount of charge in the percentage of total capacity in Coulombs held by a particular cell and the battery eventually. However, the SoC of the battery pack is the same as the lowest SoC among all cells of that battery, implying that the cells of the lowest capacity restrict the maximum charge deliverable by a battery.
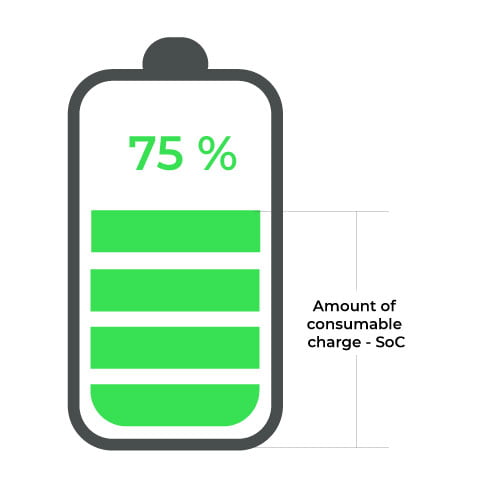
- State of Health (SoH): This factor communicates the maximum charge a cell can retain at this specific instance in its lifetime. The cell’s lifetime is defined by the number of charge-discharge cycles undergone until it reaches a specific percentage of its original capacity, after which the manufacturer recommends that the cell not be used. For example, for a cell of a particular chemistry, a certain manufacturer shall specify 800 cycles till the maximum capacity of the cell falls to 80% of its original capacity. After every charge-discharge cycle, the maximum amount of charge a cell can retain deteriorates. Therefore, SoH estimates the maximum amount of charge a cell and, eventually, the battery can retain currently.
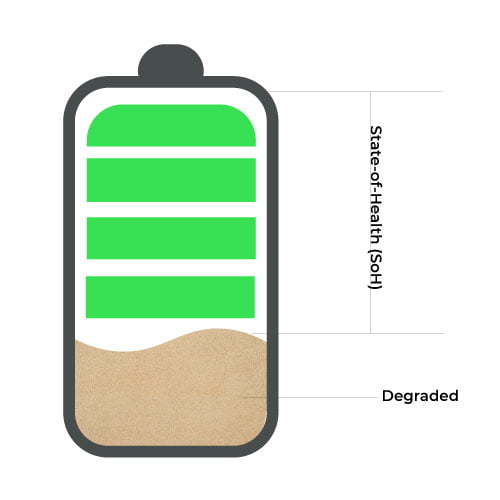
- State of Power (SoP): This factor informs about the maximum power a battery can source for the connected load and sink from it in case of regenerative braking. More specifically, the maximum power limit that the load should demand/draw out of a battery pack. This BMS estimates SoP by calculating the current limits (charge and discharge), voltage limits (charge and discharge), SoC limits (charge and discharge), and DC power in Watts. To understand the need for this factor, consider how a cell could be damaged if excessive charge gets drawn out of it beyond its maximum capacity; similarly, exceeding the power limits could damage the battery.
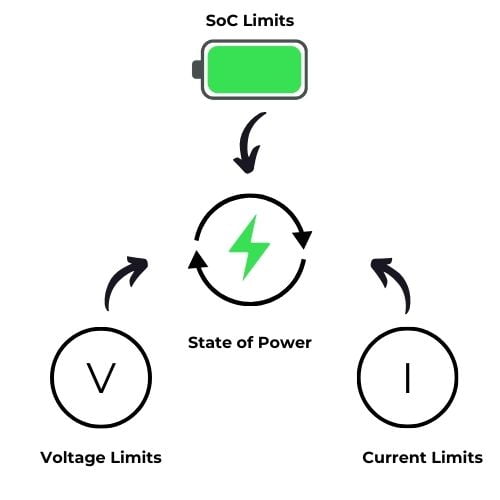
- Distance to Empty (DTE): This factor estimates how much distance an EV could cover, provided that its driving style remains the same for a prolonged duration. DTE differs from the range of an EV that OEMs advertise. While the range of any vehicle is the maximum distance it can travel from a full charge (100% SoC) up to full discharge (0% SoC), in contrast, the DTE informs about the distance a vehicle could travel from its instantaneous SoC before it reaches 0% SoC and the vehicle comes to a halt. DTE assists users in carefully planning a trip and choosing the route that features a sufficient number of charging points for the vehicle.
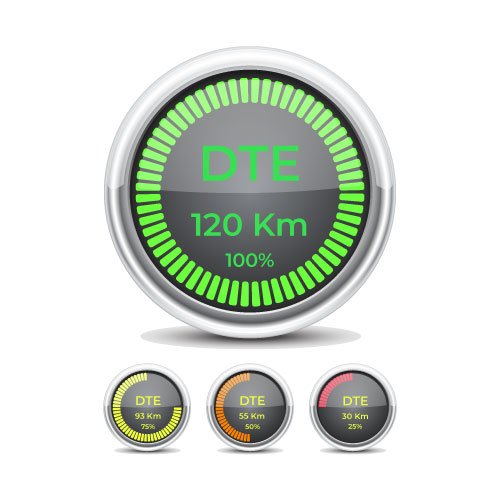
Importance of accurate estimations
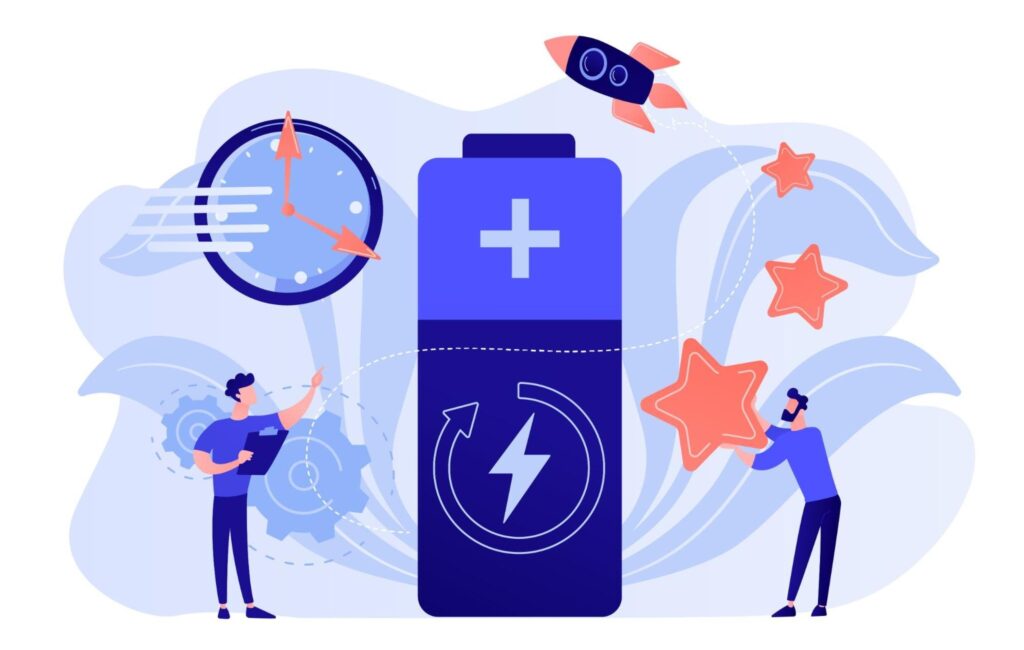
One needs estimation when a quantity is measurable and quantifiable, but sensing it directly using a physical sensor is impossible.
For example:
- Voltage is measured directly by taking a difference between the potential across any two points on an electrical conductor.
- Currents are measured indirectly by measuring the voltage across a resistor in series with the load and then calculating the currents by dividing this voltage by the known value of the same resistor.
- Temperature can also be measured indirectly by a resistance-based NTC-type sensor arranged inside a resistor-based voltage divider circuit.
However, in the case of batteries and cells, unlike the cell voltage and charge/discharge current, which you can measure and calculate accurately, there are no means to determine the instantaneous charge and a cell’s health (degradation factor). Estimation algorithms become extremely relevant in such cases.
The required accuracy of estimation is different for each algorithm:
- SoC estimation demands the highest possible accuracy because it is important to cut off a battery pack from its charger once it reaches its maximum capacity and also cut off from the load when the capacity has depleted to some alarming levels. To successfully perform these tasks during the runtime of a battery, the BMS must have accurate and precise information about the battery’s SoC.
- SoH estimation runs throughout a battery’s life cycle. This estimation works by keeping track of the number of charge-discharge cycles of the battery during the vehicle’s operation. That’s because a cell’s health gradually degrades over a long duration of its operations. Generally, it takes a few years for the battery to degrade to 80% SoH, and therefore, the estimation process is gradual, and the accuracy requirement is not as stringent as that of SoC estimation.
- SoP is calculated more than estimated but depends on the accurate measurement of current, voltage, and SoC limits during charge and discharge, which depends on SoC. Thus, it is evident once again why accurately estimating SoC is important. The required calculation accuracy for the SoP is much greater than the accuracy of SoH because the load should have a rough estimate of the power a battery pack can deliver instantly and absorb instantly in case of regen braking. Generally, high-power vehicles such as electric trucks and sports cars require a high precision for this factor. It enables a ‘Boost-mode’ feature to output greater power in situations like overtaking, traction control, climbing a hill while carrying heavy loads, and other strenuous situations.
- DTE is calculated by estimating the SoC and is also dependent on the odometry information from the vehicle. As previously stated, any inaccuracies in this calculation would lead to fewer kilometers traveled by the vehicle than its estimation. This insufficiency would eventually affect any end-user who plans trips requiring the least number of stops at the charging station. Additionally, when the stations are far apart, the user might not be able to reach the next planned charging point if the vehicle stops in the middle of the road. Therefore, the error tolerance for estimating the DTE should be as low as possible to avoid unnecessary troubles for the user.
Factors affecting the estimations
The estimation of SoP, SoH, and DTE majorly depends on the estimation of SoC, the measurement of voltages, currents, and temperatures, and the model used to estimate SoC. Therefore, we shall focus on the factors affecting the estimation of SoC and the required measurements.
- The measurement of cell and battery pack voltage depends on the accuracy of the ADC used in the circuit. Moreover, the supporting circuitry, such as the Butterworth low pass filters and EMC filtration components, tend to have their losses. These losses occur because the RLC components start degrading over time if operated under stressful conditions like elevated temperatures or frequent voltage and current spikes. The measured voltages then start exhibiting drifts, often interpreted as offsets and biases, which directly affect the measurement accuracy of the voltage and, indirectly, the accuracy of current and temperature.
- The SoC estimation algorithm requires accurate voltage and current measurement, among which the latter is more important for the Coulomb Counting method (both physical and virtual). Suppose a physical Coulomb Counting device measures incoming and outgoing charges from a battery. The large spikes and small drifts in current and other noises are the major factors affecting the inaccuracies in the estimation of SoC.
- While the Coulomb Counting method delivers more accurate results than estimating SoC from Open Circuit Voltage, obtained when the EV is stable and disconnected from any load, it has shortcomings when estimating the SoC instantaneously. Therefore, we take the help of the Extended Kalman Filter (EKF) algorithm. The EKF algorithm initially predicts SoC with the help of current and voltage limits and then corrects its estimation, thus delivering an accurate value. We will discuss the EKF algorithm in detail in our blog next month.
- SoH estimation depends on the accurate values of SoC at the start and the end of the charging process. Although an inaccurate value of SoC may not affect the SoH estimation in the short term, it will have severe integration drifts over a long duration. Similarly, SoP depends on SoC and voltages, and the same factors affect it as well.
- DTE, which depends on the vehicle’s odometry data, stays unaffected by data loss if the source channel (for example, CAN communication) gets momentarily disrupted. However, the accuracy of the odometry calculation at the source itself significantly affects it. Apart from these, the SoC estimation is also a major factor that affects the DTE estimation.
Conclusion
With an astute understanding of the significance of accurate battery parameter estimations and the critical role of a Battery Management System (BMS), it becomes easier to unlock the full potential of battery packs while ensuring their safety and optimal performance. Monitoring voltage, current, and temperature, the BMS safeguards against potential hazards and provides estimations for essential parameters such as State of Charge (SoC), State of Health (SoH), State of Power (SoP), and Distance to Empty (DTE).
Precise estimations are vital for effective battery management. SoC estimation allows for appropriate charging and discharging, while SoH estimation tracks the battery’s health over time. SoP estimation determines the battery’s power delivery capabilities, and DTE estimation aids in trip planning for electric vehicles. Accurate voltage, current, and temperature measurements are paramount for reliable estimations. Factors like the quality of the analog-to-digital converter (ADC) and circuitry losses directly influence measurement accuracy and, consequently, the overall estimation reliability.
In the upcoming blog, we will explore the methods used to estimate SoC, unveiling the innovative approaches and algorithms employed in state estimation. By understanding these techniques, one can enhance their understanding of battery management and leverage the full potential of their battery systems.